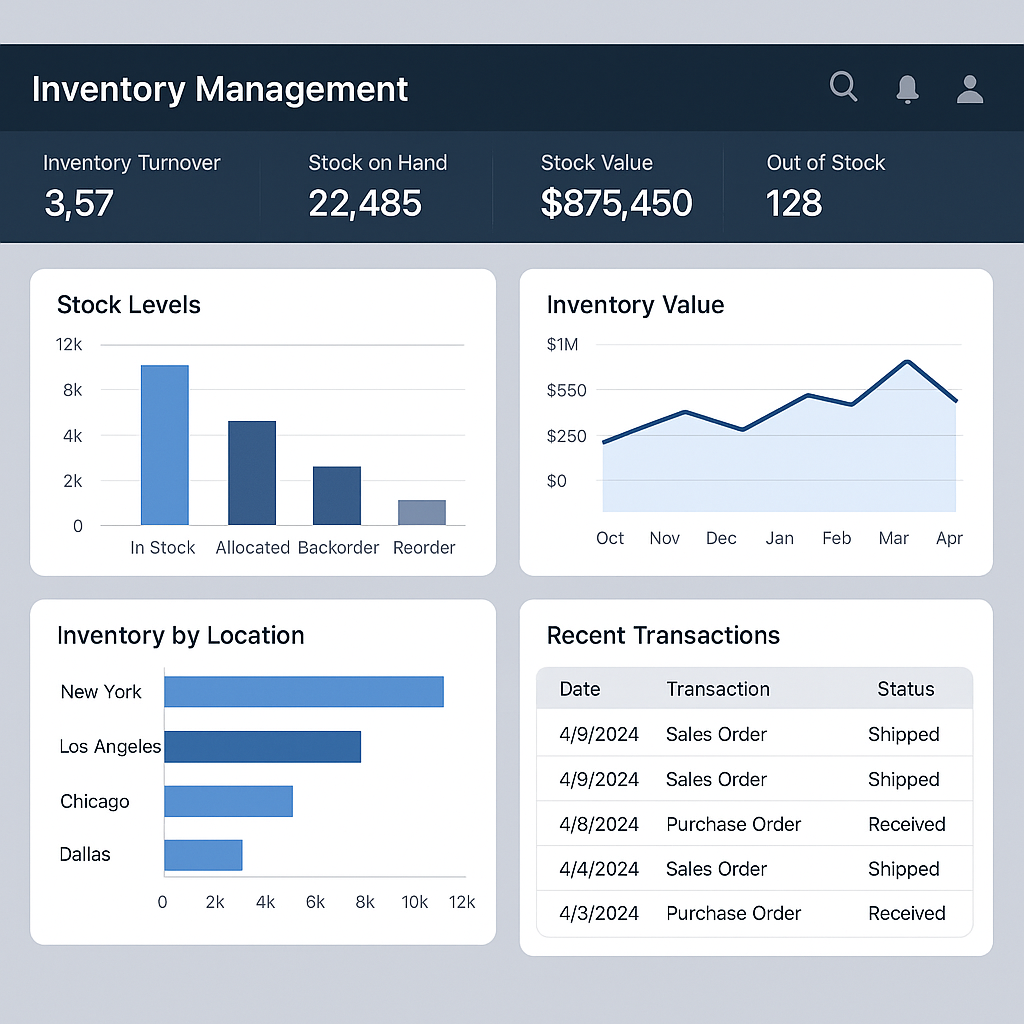
Table of Contents
The Inventory Tightrope: Operations vs. Finance
Inventory management often feels like walking a tightrope. Operations teams need sufficient stock to fulfill orders and keep production running smoothly, while finance teams focus intensely on minimizing carrying costs and ensuring accurate valuation for financial reporting. Striking this balance is crucial, and insights distilled from numerous complex system deployments indicate that integrated Enterprise Resource Planning (ERP) systems like NetSuite provide the necessary framework, though successful implementation requires careful configuration.
NetSuite approaches inventory management not as a standalone function but as a core component woven into the financial and operational fabric of the business. It offers a suite of tools designed to provide visibility and control, from item setup and costing to warehousing and fulfillment. Let’s dive into some key areas.
Foundational Item Master Data
Everything hinges on the Item Master. As highlighted in discussions around Master Data Management (MDM), consistent and accurate item setup is paramount. NetSuite allows for extensive configuration, including item types (inventory, non-inventory, service, assembly), units of measure, purchasing/sales details, and crucially, accounting-related information. Defining GL accounts for assets, Cost of Goods Sold (COGS), and income directly on the item record automates much of the downstream financial posting. Don’t underestimate the setup effort here; getting it right prevents countless headaches later.
Costing Methods: The Financial Impact
How you value your inventory directly impacts your COGS and, therefore, your profitability reporting. NetSuite supports various costing methods (Average, FIFO, LIFO, Standard, Specific), and the choice isn’t merely operational.
- Average Costing: Simple, smooths out price fluctuations, widely used.
- FIFO/LIFO: More complex to track, better matches costs to revenue (FIFO) or reflects replacement cost (LIFO), significant tax implications (especially LIFO in the US).
- Standard Costing: Excellent for manufacturing control, requires variance analysis.
The selected method must align with accounting standards (like ASC 330 in GAAP) and business strategy. Switching methods isn’t trivial, involving data conversion and potential restatements. It’s a decision requiring close collaboration between finance and operations. This involves careful consideration of revenue recognition and inventory valuation requirements under current accounting standards.
Maintaining Accuracy: Cycle Counts and Physical Inventory
Accurate records are non-negotiable. NetSuite facilitates this through:
- Cycle Counting: Regularly counting small subsets of inventory. This improves accuracy over time without requiring a full shutdown. NetSuite can help plan counts based on item velocity or value (ABC analysis).
- Full Physical Inventory: Periodically counting everything, often annually. NetSuite provides tools to record counts and post adjustments for discrepancies, directly impacting the balance sheet inventory asset value.
These processes are operationally intensive but essential for reliable financial reporting and operational planning. They provide the data integrity needed for confidence in features like NetSuite’s Fixed Assets Management, ensuring assets tracked are physically present.
Strategic Implementation Insights
Successfully leveraging NetSuite Inventory Management goes beyond enabling features. Consider:
- Process Alignment: Does the system configuration match actual warehouse processes? User adoption relies heavily on this.
- Multi-Location Complexity: NetSuite handles multiple warehouses, but transferring stock involves financial implications (in-transit inventory) and potential intercompany considerations.
- Reporting Needs: Standard reports are helpful, but custom saved searches or analytics workbooks are often needed for specific KPIs (turns, days of supply, slow-moving stock).
Advanced Inventory Analytics and Performance Optimization
Demand Forecasting Integration leverages NetSuite’s built-in forecasting capabilities combined with historical sales data, seasonal patterns, and external market indicators to optimize inventory levels while minimizing stockouts and excess inventory. Advanced implementations integrate demand planning with supplier lead times, production schedules, and financial budget constraints to create comprehensive inventory optimization frameworks that balance service levels with working capital requirements.
ABC Analysis and Classification Systems enable sophisticated inventory segmentation based on value, velocity, and strategic importance rather than simple dollar amounts. NetSuite’s flexible classification framework supports multiple dimensions including profitability analysis, supplier risk assessment, and obsolescence evaluation, enabling differentiated management approaches that allocate attention and resources based on business impact rather than treating all inventory items equally.
Inventory Performance Metrics Dashboard provides comprehensive visibility into key performance indicators including inventory turns, days sales outstanding, gross margin by item, and carrying cost analysis. Advanced reporting leverages NetSuite’s SuiteAnalytics capabilities to create executive dashboards that connect inventory metrics to financial performance, enabling data-driven decisions about product mix, procurement strategies, and working capital optimization.
Automated Reorder Point Optimization utilizes dynamic calculations based on historical usage patterns, supplier performance, and seasonality factors to maintain optimal inventory levels without manual intervention. These automated systems continuously adjust reorder points and quantities based on changing demand patterns, supplier reliability, and business growth, reducing manual planning effort while improving inventory availability and working capital efficiency.
Integration Architecture and System Connectivity
Warehouse Management System Integration connects NetSuite with specialized WMS platforms to provide detailed operational control while maintaining financial accuracy. These integrations enable real-time inventory tracking, location management, and picking optimization while ensuring that all physical movements are accurately reflected in NetSuite’s financial records, supporting both operational efficiency and financial control requirements.
Supply Chain Partner Connectivity facilitates electronic data interchange with suppliers and customers through EDI, APIs, or specialized integration platforms. These connections enable automated purchase order generation, advanced shipping notifications, and real-time inventory visibility across the supply chain, reducing manual processing while improving accuracy and responsiveness to supply and demand changes.
Manufacturing Integration Patterns coordinate inventory management with production planning, shop floor control, and quality management systems. NetSuite’s manufacturing capabilities integrate directly with inventory tracking to provide real-time visibility into work-in-process, component consumption, and finished goods availability, enabling more accurate production planning and financial reporting.
Third-Party Logistics Integration supports complex fulfillment models including dropshipping, third-party fulfillment, and consignment inventory through specialized integration patterns that maintain inventory visibility and financial control while leveraging external operational capabilities. These integrations require sophisticated tracking of inventory ownership, location, and valuation across multiple parties.
Financial Controls and Compliance Framework
Inventory Valuation and Costing Controls implement comprehensive controls around inventory valuation including automated variance analysis, cost standard maintenance, and lower-of-cost-or-market adjustments. Advanced implementations leverage NetSuite’s workflow capabilities to route significant variances for management review while automatically processing routine adjustments within established parameters.
Audit Trail and Documentation Management maintains comprehensive records of all inventory transactions including receipts, issues, transfers, and adjustments with complete user attribution and business justification. These audit trails support both internal control requirements and external audit procedures while providing transparency into inventory management decisions and their financial impact.
Segregation of Duties Implementation establishes appropriate separation between inventory custody, recording, and authorization functions through NetSuite’s role-based security framework. Effective implementations ensure that individuals responsible for physical inventory management cannot modify system records without appropriate approval, while maintaining operational efficiency through streamlined processes.
Regulatory Compliance and Reporting addresses industry-specific requirements including FDA traceability, hazardous materials management, and international trade compliance through specialized configurations and reporting capabilities. These compliance frameworks integrate with standard inventory processes to ensure regulatory adherence without creating operational bottlenecks.
Strategic Optimization and Continuous Improvement
Inventory Investment Optimization analyzes the relationship between inventory investment and business performance through comprehensive financial modeling that considers carrying costs, stockout costs, and opportunity costs. Advanced analyses leverage NetSuite’s financial data to identify optimal inventory investment levels by product category, supplier, and market segment while supporting growth objectives.
Supplier Performance Management integrates inventory management with vendor performance evaluation including delivery reliability, quality metrics, and cost competitiveness. These analytics enable strategic sourcing decisions based on total cost of ownership rather than purchase price alone, supporting supplier development and relationship management initiatives.
Product Lifecycle Management coordinates inventory strategies with product launch, maturity, and discontinuation cycles to minimize obsolescence while maximizing availability during critical periods. These approaches integrate with marketing, sales, and engineering functions to ensure inventory decisions support broader product strategy and financial objectives.
Continuous Process Improvement establishes systematic approaches to inventory management optimization through regular performance review, best practice identification, and process enhancement initiatives. These improvement programs leverage NetSuite’s extensive reporting capabilities to identify optimization opportunities while building organizational capabilities for ongoing inventory management excellence.
NetSuite offers robust inventory capabilities that extend far beyond basic stock tracking to encompass comprehensive financial control, operational optimization, and strategic decision support. Realizing their full value demands a strategic approach that harmonizes operational requirements with financial controls and reporting standards while leveraging advanced analytics and integration capabilities.
Successful implementations require ongoing attention to process optimization, system configuration, and user training rather than treating inventory management as a one-time setup exercise. Organizations that invest in comprehensive inventory management capabilities position themselves for sustainable competitive advantage through superior working capital management and operational efficiency.
How does your organization balance operational inventory needs with financial scrutiny? Share your insights or connect with me on LinkedIn to discuss further.